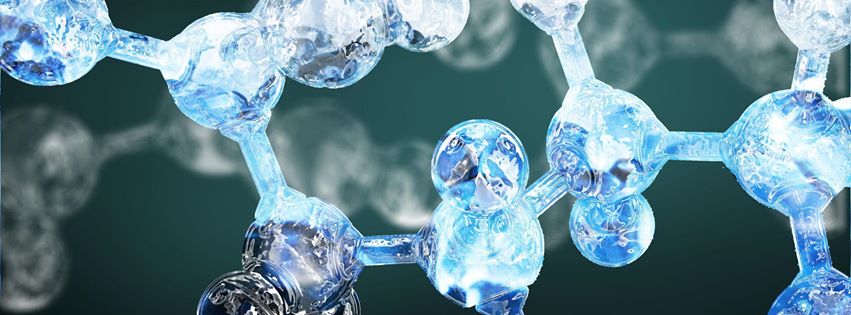
В этой серии статей будут раскрыты многие вопросы, встающие перед теми, кто печатает на FDM принтерах, и будет предложен комплексный подход к их решению.
В сети в целом, и тем более на этом ресурсе в частности, есть огромное количество информации о том, как тот или иной печатник решает возникшие перед ним проблемы 3D-печати. Но несмотря на то, что информации о способах решения различных задач довольно много, раз за разом у новичков, да и у людей опытных возникают одни и те же вопросы при смене принтера, пластика, сопла или даже размера печатной модели.
Даже самые, казалось бы, отработанные схемы и подходы терпят крах, и создается впечатление, что 3D-печать это некое колдовство, шаманизм, и без бубна и покровительства высших сил тут делать нечего. Соответственно и социальная активность мейкеров в блогах зачастую напоминает мелкофеодальное соперничество кланов "ПЛАпоклонников" и "АБСоведов" с мелкими вкраплениями просветленных "Филаментаристов" и "Дзен-фотополимерщиков". Что касается последних, то они святы, и речь о них в этой статье не пойдет.
Остальные же, как это ни парадоксально, правы во всем своем великом и разнообразном множестве. Да, правы все!
Но откуда столько раз за разом повторяющихся вопросов? И чем объяснить столь великое число различных способов решения одних и тех же проблем?
Автор в моем лице решил взять на себя труд и ответственность обозначить некий путь для всех и каждого, пройдя которым один раз, можно обрести понимание не столько способов решения разрозненных вопросов, сколько структуру и принцип нахождения решений для нестандартных задач. То есть, эту серию статей можно рассматривать как обобщающе-образовательную, и цель её написания - системная подача проверенных знаний, в противовес сонму укоренившихся "голубиных суеверий".
Американский психолог Скиннер ставил такой эксперимент. Сажал голубя в клетку и через равные (!) интервалы времени сыпал в клетку корм. Что же стали делать голуби? Удивительно, но они решили, что от их поведения зависит, получат они корм или нет. И они стали делать точно то, что они делали сразу перед появлением корма. Например, если голубь прятал голову под крыло, а потом появился корм, такой голубь начинал постоянно прятать голову под крыло – в надежде, что появится еда.
На этом предисловие можно считать законченным. Теперь перейдем к азам, без усвоения которых невозможно в полной мере понять и усвоить нижеприведенную информацию.
Полимеры.
Что такое полимеры? Я долго боролся с искушением процитировать тут статью из Википедии, но все же отчасти победил это желание, и попытаюсь там, где это возможно и оправдано, писать своими словами.
Прежде всего, отличительным свойством полимеров, и во многом определяющим их механические свойства, является размер молекул, из которых они состоят - макромолекул. Каждая молекула полимера состоит из цепочки соединенных между собой мономерных звеньев. Чем больше этих звеньев в молекуле, тем соответственно большим молекулярным весом она обладает. Тем выше степень полимеризации.
Виды полимеров.
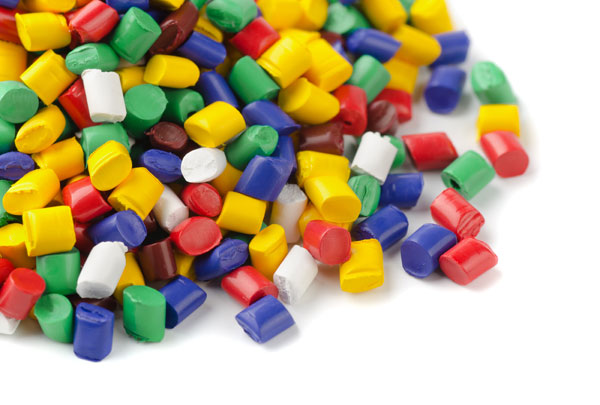
Полимеры делятся на 2 большие группы: термопласты (именно о них и пойдет дальше речь) и реактопласты.
Если не упоминать сложные слова про "силы Ван-дер-Ваальса", которые объединяют между собой молекулы термопластов, в отличие от химических связей в реактопластах, то условно их основное отличие можно определить, как возможность или невозможность многократного размягчения и переработки полимера.
К реактопластам относятся, к примеру, всем знакомые эпоксидные и полиэфирные смолы. Растворить, расплавить или переработать их заново, увы, нереально.
Термопласты как раз относятся к тем полимерам, которые могут многократно перерабатываться и формоваться без существенных структурных изменений и ухудшения их механических характеристик.
Тут стоит заметить, что вторичное сырье, это отнюдь не второй раз размягченный термопласт! Что уж там далеко ходить, тот самый всем нам знакомый филамент для 3D-печати попадает в руки мейкеров в лучшем случае дважды переработанным: первый раз в гранулы, второй раз в пруток из этих гранул. А "в лучшем" потому, что в погоне за упрощением технологии и удешевлением конечного продукта некоторые производители могут использовать уже окрашенный гранулят, а это, как минимум, еще одна стадия переработки, потому что изначально при выработке все полимеры либо бесцветные, либо имеют свой не самый нарядный оттенок.
Ну и конечно совсем уж нещадно можно удешевить филамент, используя вторичное сырье... Да, из вторсырья малореально получить ровный по диаметру пруток по той простой причине, что свойства расплава будут неоднородными по массе, отсюда неравномерное давление в промышленном экструдере, неравномерная пластичность расплава и его усадка. Соответственно, и при печати такой пруток будет себя вести совершенно непредсказуемо... Но зато его цена будет просто сказочной.
Впрочем, я отвлекся!
Из вышеописанного самое главное, что надлежит усвоить, это то, что молекулярная масса (далее ММ) полимера имеет существенное, а во многом и определяющее значение, обуславливая такие свойства полимера, как его текучесть, ударостойкость и в целом прочность конечного изделия.
Также в этой главе стоит упомянуть, что есть две основные группы термопластов, выделяемые по типу построения макромолекулы:
Гомополимеры (состоят из одинаковых по составу повторяющихся мономерных звеньев),К гомополимерам можно отнести гомополимер стирола - полистирол (PS) или гомополимер пропилена - полипропилен (PP).Сополимеры (цепочки молекул которых состоят из двух или более различных структурных звеньев).К этой группе относятся, например, акрилонитрил-бутадиен-стирол (ABS).
Среди сополимеров в свою очередь выделяются блок-сополимеры. (макромолекулы которых состоят из регулярно или статистически чередующихся гомополимерных блоков, различающихся по составу или строению.)
К числу блок-сополимеров, относятся термоэластопласты, макромолекулы которых состоят из блоков термопластов (полистирол, полиэтилен, полипропилен) и гибких блоков эластомеров (полибутадиен, полиизопрен, статистические сополимеры бутадиена со стиролом (PBS) (SBS) (SBR) или этилена с пропиленом (EPDM)).
Проще говоря, это различные синтетические каучуки термоэластопласты (ТЭП).
Виды термопластов.
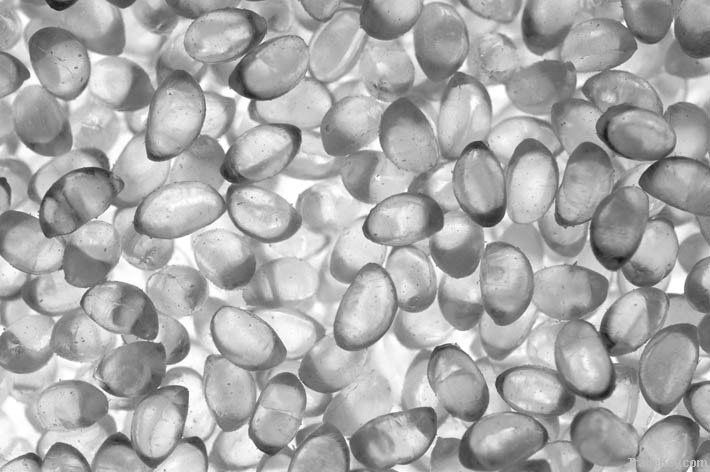
Термопласты, которые как раз и представляют для нас интерес, можно условно разделить еще на 2 основные группы:маморфные и частично кристаллизующиеся.
К аморфным термопластам относятся, полистирол (PS), ударопрочный полистирол (HIPS). Все виды термоэластопластов (ТЭП). Аморфные термопласты в неокрашенном состоянии, в принципе, прозрачны, как стекло.
Всем знакомый акрилонитрил-бутадиен-стирол (ABS) различается по своему строению и бывает двух типов: с аморфной имчастично кристаллизованной структурой.
К частично кристаллизующимся полимерам относятся полипропилен (PP), полиэтилен (PE), полиамиды (PA 6, PA 66 - тот самый нейлон ), полиэтилентерефталат (PET).
Важным для нас отличием этих двух групп полимеров друг от друга является их усадка!
Кристаллизующиеся материалы имеют высокий уровень усадки и анизотропии усадки, что намекает нам на то, что напечатанные из этих пластиков изделия будут трещать и коробиться наиболее жестоко. Особенно это заметно на примере полиамида (нейлона)- усадка 1.5-2.5%, полипропилена (PP) - усадка 1.8-2.5% или полиэтилена (PE) - усадка 2.0-5.0%!
Усадка ABS колеблется от 0.4 до 2.0% в зависомости от марки. Усадка полистирола (PS) от 0.4 до 0.8%. Усадка бутадиен-стирольных каучуков и HIPS во многом зависит от содержания в их составе стирола и способа их полимеризации и составляет в зависимости от марки 0.3-2%
Усадка пластиков Filamentarno! составляет 0.3-1.3%
Особняком от этой многочисленной компании полимеров стоит PLA (полилактид молочной кислоты). Это странное вещество, в отличие от всех перечисленных выше, получают полимеризацией лактида, который в свою очередь получают поликонденсацией молочной кислоты. Несмотря на все эти молочности, к творогу и коровам этот продукт имеет мало отношения. Однако, так же как и йогурты, не все полилактиды одинаково полезны.
Существует устоявшееся мнение, что это самый что ни на есть разнатуральный продукт и его можно чуть ли не кушать ложками. Но на деле это конечно не так. Существует несколько разновидностей PLA с самым разнообразным спектром свойств и сильно отличающимися физико-механическими характеристиками. А все дело в том, что молочная кислота, равно как и лактид, будучи органическими веществами, обладают одной забавной особенностью: стереоизомерией. То есть при одном и том же составе молекулы и тех же связях они могут быть зеркальными относительно друг друга, как крылья бабочки. И свойства этих веществ могут кардинально отличаться, и отличаются.
Так например есть L-лактид, а есть D-лактид. L-лактид в чистом виде это кристаллизующийся полимер со всеми вытекающими из этого недостатками описанными чуть выше и ярко выраженной зоной стеклования. Тогда как равная смесь этих стереоизомеров дает на выходе аморфный полимер - то есть не имеющий температуры плавления как таковой, так нет и процесса его кристаллизации.
Возвращаясь чуть назад, напомню, что лактид получается из молочной кислоты и в процессе его получения в качестве катализатора используется октаноат олова, дозируемый в соответствии с остаточной концентрацией молочной кислоты. И тут важно понимать, что только от производителя полимера зависит насколько чистым будет конечный продукт, каков будет его изомерный состав и, соответственно, каковы будут его физико-механические характеристики.
Гигроскопичность полимеров
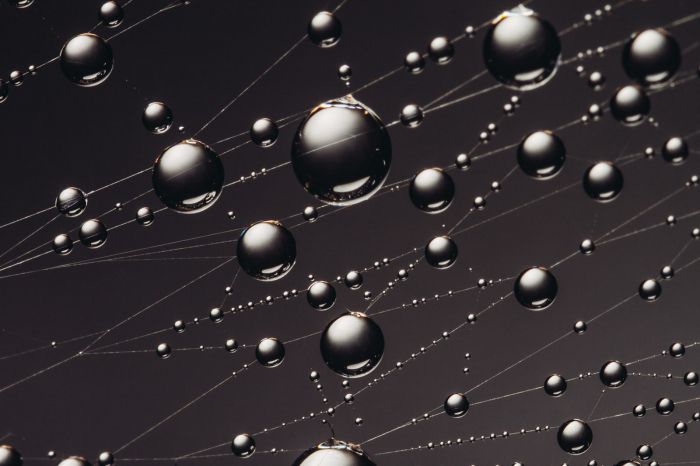
Если сложить все те копья, которые были сломаны на почве влажного пластика и скрепить их теми теми мыслительными усилиями, которые были потрачены на борьбу с этим явлением, можно наверное построить лестницу до луны!
А всему тому виной неотъемлемое свойство некоторых полимеров впитывать влагу.
Вода, как все знают, очень любит кипеть при нагревании, а при кипении превращается в пар - то есть совершает фазовый переход. И переход этот сопровождается неслабым расширением. И ладно, когда этот переход происходит в бане или в гейзерах Камчатки - первое полезно, а второе красиво - но когда этот процесс начинается в экструдере 3D-принтера, происходят вещи мало приятные. Щелчки при печати, сопровождаемые пропусками экструзии и дырами в периметрах, неравномерность экструзии, пенообразование и прочие не эстетичные процессы доставляющие немало головных болей печатникам.
Уже немало сказано и написано на тему как хранить и сушить филамент, но вот беда - если при производстве прутка был пропущен важный технологический этап сушки гранулята (конечно с целью удешевления производства), который занимает для ABS от 4 до 6 часов горячим воздухом при температуре 80С (а кому охота?) или этот этап сокращен, то на выходе получается филамент, содержащий образованные расширяющейся влагой пузырьки, вмещающие водяной пар. И вытащить его оттуда сушкой в духовке крайне сложно...
Итак, кто же у нас самый большой любитель впитать воду при первой возможности?
Первое место в номинации на звание
Второе место уверенно занимает PA-66 (полиамид, он же нейлон) с результатом 0.4% от собственного веса.
Третье место занимает ABS со средним результатом 0.2%
И совсем уж аутсайдером в поглощении влаги на фоне этих непревзойденных мастеров выглядят пластики Filamentarno! со своими смешными 0.07% поглощения влаги даже в условиях водной среды )) Даже если вы будете хранить его в ванной, даже если вы наполните эту ванную водой, то проблем с печатью не возникнет. Просто стряхните с него капли перед использованием

На этом краткий обзор применимых для 3D-печати методом FDM полимеров можно считать завершенным.
Занудные химики-полимерщики на этом месте бы наверное сказали, что все это попса и они сильно разочарованы, но в мои цели не входило писать трактат или диссертацию на тему, а лишь ознакомить читателей для начала с общей картиной, написанной широкими мазками. Надеюсь, кто-то дочитал до этого места, так как дальше пойдет пободрее и с картинками!

Итак, переходим к следующей главе:
Что такое ПТР, при чем тут молекулярная масса полимера (ММ) и как это все связано с усадкой при печати?
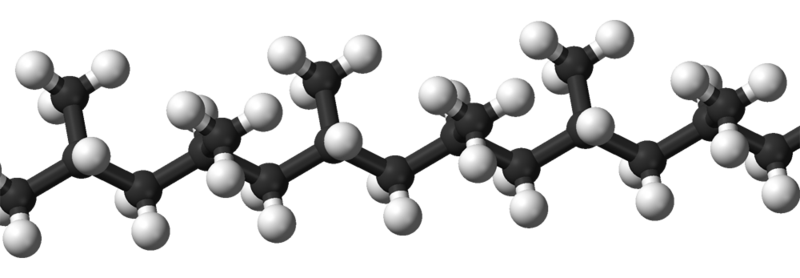
Наверное многие из вас, бродя по просторам интернетов в поисках ответа на то, почему жизнь такая пластмассовая, натыкались на это загадочное сокращение: ПТР.
На самом деле ПТР это Показатель Текучести Расплава, так что с одной стороны ничего загадочного в нем нет. Говоря по-простому: цифра, стоящая после этих букв, указывает сколько грамм нагретого до определенной температуры полимера может вытечь под воздействием определенной массы груза через отверстие определенного размера за 10 минут.
Да, по-простому не получилось... Но на самом деле, ПТР это те еще Попугаи Традиционной Реологии поскольку если вы знаете только цифру, то вы не знаете о реологии полимера ничего! И все потому, что к разным полимерам применяют разные технологии измерения этого странного параметра.
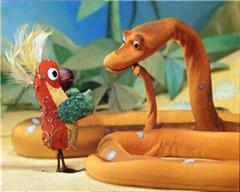
Особенно наглядно это видно на примере ABS пластика, где для измерения одного и того же полимера может быть применено 3(!) разных способа, (Можно использовать груз массой 5 кг при температуре 200°С, груз 3,8 кг при 230°С или груз 10 кг при 220°С.) которые дадут 3 разных(!) результата. Как вам эти точные науки? )))
Впрочем, вам, уважаемые печатники, в это вникать и не стоит. Все это головная боль производителей прутка! Если конечно у производителя есть чему болеть и он не просто "давит лапшу из АБС" (С), а пытается создать достойный продукт, которым удобно пользоваться.
Но все же я упомянул тут ПТР не зря. Если и вправду по-простому, то эта цифра определяет насколько расплав полимера густой. И чем эта цифра в граммах/10 минут меньше, тем, соответственно, полимер гуще. А чем полимер гуще, тем сложнее его продавить сквозь маленькое отверстие сопла экструдера 3D принтера.
Вы уже готовы сказать: "Ура, теперь я все понял - чем больше тем лучше!" - но не спешите с выводами! Все дело в том, что косвенно низкий показатель ПТР говорит о бОльшей молекулярной массе полимера. Как я уже писал выше, именно молекулярная масса полимера во многом определяет его механические свойства. В частности, прочность и ударостойкость. И вот тут все с точностью до наоборот - чем ПТР меньше, тем лучше.

Как это часто случается в жизни, нет идеальных решений - есть компромиссные. На графике как раз и отображены муки выбора марки пластика производителем и указана зона возможного компромисса между прочностью и возможной скоростью печати в зоне пересечения двух областей.
Голубая область отражает зависимость между возможной скоростью (Vp) печати и текучестью расплава полимера (ПТР) Розовая область отражает зависимость между показателем ПТР и молекулярной массой (MМ).
Так как полимеры являются не ньютоновскими жидкостями, то к счастью для нас их текучесть растет с повышением скорости потока, что отчасти компенсирует уменьшение скорости печати с ростом молекулярной массы, расширяя границы применимости различных полимеров для 3D-печати.
*график дан для наглядности, точных значений тут искать не следует!
Казалось бы, и все на этом? Но не зря была помянута усадка!
Наверное каждый из вас сталкивался с проблемой, когда прутком какого-нибудь производителя просто нереально печатать при адекватных температурах! Приходится задирать ее все выше и выше, чтобы слои хоть как-то спекались и чтобы не было пропусков и недоэкструзии. Почему так случается, и что в физическом смысле несет повышение температуры печати?
Все дело в том, что как наверное заметил внимательный читатель, ПТР штука весьма относительная, и зависит этот показатель еще и от температуры расплава. Чем она выше, тем текучесть выше, и тем легче двигателю экструдера на принтере протолкнуть расплав через отверстие сопла.
Но не спешите в очередной раз кричать: "Ура, вот теперь я точно все понял!" ))) - потому как взять инженерный пластик с высокой ММ и низким ПТР и печатать им на 260C конечно можно... Но несмотря на его казалось бы высокую прочность, ожидаемую в связи с высокой ММ, ваша распечатка разлетится по слоям! И это случится потому, что тогда как межслоевая адгезия (а тем паче адгезия к печатному столу принтера!) имеет свои финальные значения, то тепловое расширение аморфных полимеров с увеличением температуры не прекращается вплоть до начала его термической деструкции. Для ABS пластиков она начинается в районе 260C, для пластиков Filamentarno! 250C, для ПЛА это уже 220-230C.
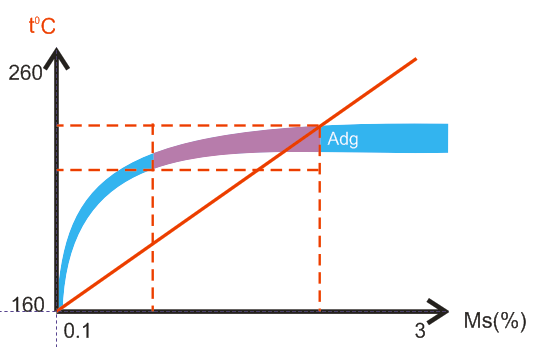
На этом рисунке наглядно показан график роста адгезии с ростом температуры (t) и график термического расширения/последующей усадки (Ms - molding shrinkage). Зоной с наилучшим соотношением этих двух параметров можно считать выполаживание кривой роста адгезии (Adg).
*график дан для наглядности, точных значений тут искать не следует!
Резюмируя, могу посоветовать не печатать при темературах, больших, чем минимально достаточные для хорошей адгезии между слоями.
На этом, на мой взгляд, можно и закончить часть про полимеры и их переработку, чтобы ненароком не рассказать каких-нибудь важных производственных секретов и технологических тонкостей... А вы думали, что я рассказал всё?

Спасибо за внимание! Как только я снова смогу потратить еще один день на написание статьи, будет вторая часть.
Она будет посвящена дефектам печати, и способам их устранения с учетом изложенного выше, а также качеству филамента и тому, как и почему оно влияет на печать. Будет много математики и скучных формул... Шучу

Спасибо тем, кто прочел этот текст от начала и до конца!
комментарии